SERVICEABLE RANGE
The basic request, detail design, process and quality test of FENFA Silicone Sealants are included in this installation guide, which is suitable for FENFA Silicone Sealants except Silicone Structural Sealants produced by FENFA rubber products Co., LTD.
BASIC REQUEST
1. The users can obtain reliable products and cogent technical assistance when they buy FENFA Silicone Sealants from FENFA rubber products Co., LTD or the appointed sales agencies.
2. The operating personnel must be familiar with the fundamental characteristic of Silicone Sealants, understand the method to eliminate the sealing failure and the mix proportions of Silicone Sealants, because the sealing quality depends on the responsibility and qualification of operating personnel.
3. The optimal construction condition is that the temperature is between 15℃ and 27℃ and relative humidity is between 40% and 80%. The temperature should not exceed 4℃~40℃ and the relative humidity should not below 30%. The construction can’t be proceeding in rain or snow.
4. The adhesion test, consistency test and pollution test should be carried out by FENFA rubber products Co., LTD for the special building materials, new materials, and materials with surface coat and surface treatment. Silicone Sealants could be used with appointed method after the serviceable report is providing by FENFA rubber products Co., LTD.
5. The temperature, humidity, date and time of the construction, the trademark, production date and batch number of the Silicone Sealants, with or without primer, clearing process and the name of the operator must be recorded.
6. The users should contact with the technical section quickly if there are quality or technical questions in the construction process and you can obtain circumspect technical service in time. The construction process should be stopped before when there is grave quality question and the process can continue if the information is obtained from the technical section.
DESIGN REFERENCE
1. General description
The basis materials, bottom paint, gasket materials, binding spacer and sealant are central factors when the sealant is used to seal the joints, as show in Figure 1.
2. The basis materials
a. Brick, concrete, ceramic materials, marble, metal, glass, plastic, wood, etc, are building materials in common use with or without pores. Some materials can bond well with the sealant after the surface is treating with physical or chemical method.
b. The protective coating of metal and the waterproof of concrete will affect the bond quality between sealant and basis materials. It is difficult to find the protective coating when the bond quality is badness or the bond interface is damage. Therefore, in order to determine the treating method or the suitable bottom paint, the user should contact with us or the manufacturer of the basis materials. Adhesion test and compatibility test are necessary in sometimes.
3. The bottom paint
The bottom paint can improve the bond quality between the sealant and the basis materials. There is good bond quality between FENFA Silicone Sealants and most basis materials without the bottom paint. The user must use the appointed bottom paint when the bottom paint is necessary marked by FENFA rubber products Co., LTD in adhesion test and compatibility test.
4. The gasket materials
In order to ensure the joint design and the bond quality, it is necessary to select and use the suitable gasket materials. The function of the gasket materials as follow(shown in Figure 2):
a. To control the depth and shape of sealant in the joint.
b. Sealant can wet the basis materials surface completely with the gasket materials.
c. It can be used as the temporary seal course when the condition is not suitable to brush sealants immediately or the sealant is out of work.
Saturated materials, asphalt and materials without sulphuration will pollute the basis materials and sealants, so they can’t be used as the gasket materials. Polyurethane foam, polyethylene foam and sponge rod are recommended to use as the gasket materials because they are no-permanent deformation, no-water absorption, no-air-breathing, no-thermal expansion in joints. The gasket materials should not restrict the movement of sealant. In order to avoid water absorption, sealant should be brush in time. The sizes of unicellular gasket materials should be 25-30% greater than the joint width and the sizes of opening pore gasket materials should be 40-50% greater than the joint width.
5. The binding spacer
The binding spacer is used to prevent the contact between sealant and the undesirable surface or materials. The contact will damage the bonding quality of sealant (as shown in Fig.3). Polyethylene, Teflon seal or bond breaker recommended by us can be used as binding spacer. The liquid binding spacer is not recommended because that it will pollute the binding surface. In order to prevent there-surface binding, the binding spacer should be put on the non-deformation gasket material at the joint bottom. The soft gasket materials with open pores can deform easily, which will not restrict the sealant movement. The binding spacer is unnecessary in this condition. Saturated materials, asphalt and materials without sulphuration can’t be used as the gasket materials.
6. The shape and size of joints
The shape and size of joints is related with its appearance, space, displacement and the construction method, displacement ability of sealants. Several typical sealing forms of joints are shown in Fig.1, Fig.2 and Fig.3.
a. The width of sealants
The width of sealants is twice greater than the thickness and we can calculate the width of sealants based on section 4.3.9 in JGJ 102-2003.
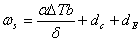
Where ωs is the joint width (mm); α is the linear expansibility of panel materials (1/oC); ΔT is the temperature difference of the curtain wall in one year (oC) and 80oC is recommended. δ is the displacement ability of sealants; b is the side length of panel in calculated direction (mm); dc is the construction deviation (mm) and 3mm is recommended; dE is the performed size considered the earthquake and other factors (mm) and 2mm is recommended;
Example 1: the length of glass panel is two meters, the liner expansibility is 1.0×10-5 /℃, the anticipative temperature difference is 80℃, the construction deviation is 3mm, the displacement ability of sealants is 12.5%.
b. The depth of sealants
The depth of sealants is related to its width. The liner expansibility of building materials, the construction season and the limiting temperature should be considered adequately when we design the joint width.
① The minimum width and depth of sealants is 6.0mm.
② The width of sealants must be larger than the depth.
③ The depth of sealants is in the same size as the joint width when the joint width in concrete, bricking-up and stone materials is less than 13mm; The depth of sealants is half of the joint width when the joint width is between 13 and 25mm.
④ The depth of sealants is greater than 6.0mm when the joint width in non-porous materials (such as metal and glass) is between 6.0 and 13.0mm; The depth of sealants is between 6.0 and 13.0mm.
SEALANT APPLICATION
1. Surface cleaning of basis materials
Surface cleaning of basis materials can be carried out based on the methods in Installation Guide for FENFA Silicone Structural Sealants.
2. Application of masking liquid at bottom
Application of masking liquid at bottom can be carried out based on the methods in Installation Guide for FENFA Silicone Structural Sealants.
CONSTRUCTION PROGRAM OF SEALANTS
1. The temporary adhesive tape can be pasted to protect the place around the cleaned surface of basis materials.
2. In order to ensure the sealants ejected from the muzzle are continuous and cylindrical, the sealants should be injected into the joints continuously; the diameter of muzzle should be less than the joints thickness, so that the muzzles can arrive at 1/2 depth of the joints. The movement of muzzle should be slow, which ensures that the sealants in joints are full and there are no gas bubble or cavity in the joints.
3. Modification should be carried out immediately after the injection of sealants has been completed. In order to confirm that the contact between the sealants and the basis materials is sufficient, the excess sealant should be put into the joints by applying a positive pressure with tools. The temporary adhesive tape can be removed.
4. The joint shouldn’t have great displacement in 48 hours because the sealants haven’t solidified completely.
CHECKING OF CONSTRUCTION QUALITY
1. Appearance checking
In order to ensure there is no bubble or cavity in the joint, appearance checking should be carried out on the basis materials surface after the construction was complete. The position in joints should be cut and filled with sealants in time if there are bubbles or cavities.
2. The skin drying test, the solidification time test and the rebound test
In order to confirm the leveling-up time and the complete solidification time, the skin drying test, the solidification time test and rebound test should be carried out for each batch. The test method can refer to the skin drying test, the solidification time test and the rebound test in Installation Guide for FENFA Silicone Structural Sealants.
3. The quality checking of two-component sealants can refer to the butterfly test, the time of tensile failure and the peel cementation test in Installation Guide for FENFA Silicone Structural Sealants.
REQUIREMENT OF ADHESION TEST, COMPATIBILITY TEST AND POLLUTION TEST
1. Adhesion Test
The number of glass or other plate in the adhesion test should be greater than there and the size is 150mm×75mm.
2. Compatibility Test
The compatibility test should be carried out for the assistant materials (such as glue tape and foam rod) in the construction process; the length of each material in test shouldn’t be less than 100mm.
3. Pollution Test
The number of samples is there and the size is 250mm×250mm.
4. The samples should be preventing to drop out and damage in package when the samples were sent by EMS.
5. The test period is 35 days. The test will be carried out in time after we receive all materials. The preliminary results will be sent to the user by fax and the formal results will be sent to the user in time.
Attentions: The information in this paper is correct. The users should understand the productions minutely and determine the optimal using method. The productions dispatched satisfy the product description, which is the unique assurance by us. The payment of goods can be sent back or the unqualified product can be replaced if we disobey the assurance. We don’t take charge of any indirect and incident damage.
|